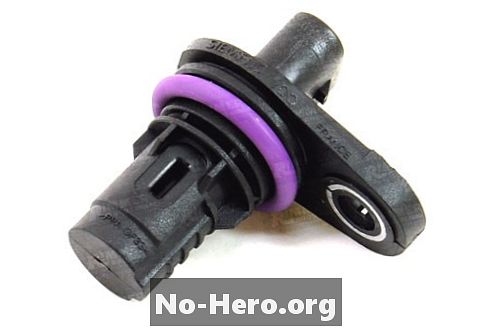
Inhalt
Fehlercode | Fehlerortung | Wahrscheinliche Ursache |
---|---|---|
P0368 | Nockenwellenpositionssensor (CMP) B, Eingang für hohen Stromkreis von Bank 1 | Kurzschluss nach Plus, CMP-Sensor, ECM |
Was bedeutet Code P0368?
Wenn ein Code P0368 mit einer Störungsanzeigelampe (MIL) in Ihrem Fahrzeug geliefert wird, hat das Steuergerät für Antriebsstrang (PCM) ein Problem mit dem Positionssensor (oder dem Schaltkreis) der Auslassnockenwelle für Motorgruppe 1 festgestellt. Bank 1 stellt die Bank des Motors dar, die den Zylinder Nummer eins enthält. Sensor B zeigt an, dass die Fehlfunktion im Nockenwellensensorkreis der Auslassnockenwelle auftritt.
Das PCM verwendet die Eingangssignale des / der Nockenwellensensors / -sensoren und des Kurbelwellensensors, um die Position und Umdrehungen pro Minute (RPM) dieser wichtigen Motorkomponenten zu überwachen, Zeitschwankungen zu verwalten und die Kraftstoffzufuhrstrategie abzubilden. Es ist klar, dass Abweichungen in der Motorkonfiguration die Anzahl der erforderlichen Nockenwellensensoren bestimmen. Zum Beispiel; Ein Überkopfventilmotor ist normalerweise mit einem einzigen Nockenwellensensor ausgestattet, da der Motor nur eine Nockenwelle hat. Ein Vierzylindermotor mit obenliegender Nocke hat wahrscheinlich auch nur einen Nockenwellensensor (da er nur eine Motorbank hat), eine obenliegende Nocke V6 erfordert jedoch mindestens zwei Nockenwellensensoren (einen pro Motorbank).Ebenso sind für einen V8-Motor mit zwei obenliegenden Nockenwellen vier Nockenwellensensoren erforderlich, da zwei Motorbänke mit zwei Nockenwellen in jeder Bank vorhanden sind.
Jeder Nockenwellensensor hat eine Schaltung (oder Schaltungen), die dazu bestimmt ist, das PCM mit individuellen Eingangssignalen zu versorgen. Nockenwellenposition und Nockenwellendrehzahl werden mit der Drehzahl und Position der Kurbelwelle verglichen, um Motorschäden zu vermeiden und den Zündzeitpunkt und die Kraftstoffzufuhrstrategie zu berechnen. Da sich die Nockenwelle (n) mit der halben Drehzahl der Kurbelwelle drehen, ist es wichtig, dass das PCM in der Lage ist, zwischen Einlass- und Auslasshüben (Umdrehungen) des Motors zu unterscheiden. Dies geschieht auch mit dem Nockenwellensensor.
Ich möchte alle systembezogenen Kabelbäume und Steckverbinder einer Sichtprüfung unterziehen, bevor ich mit den Tests beginne. Kabelkreise, elektrische Sensoren und / oder Steckverbinder, die mit Motoröl, Kühlmittel oder Servolenkungsflüssigkeit verunreinigt wurden, sollten sorgfältig auf Beschädigungen untersucht werden. Flüssigkeiten auf Erdölbasis können die Schutzisolierung der Verkabelung beschädigen und zu Kurzschlüssen oder Unterbrechungen und einem gelagerten P0368 führen. Dies ist auch eine gute Zeit, um die Batterie zu testen, die Enden und Kabel der Batterieklemmen sowie den Generatorausgang zu überprüfen.
Schließen Sie nun den Scanner an den Fahrzeugdiagnoseanschluss an und rufen Sie alle gespeicherten Fehlercodes und Standbilddaten (falls verfügbar) ab. Ich schreibe diese Informationen gerne auf, da sie hilfreich sind, wenn sich herausstellt, dass der Code nur sporadisch vorkommt. Einige Scanner verfügen auch über einen DVOM und ein Oszilloskop mit integrierten Testleitungen. Wenn Sie diese Art von Scanner erhalten können, ist dies die beste Wahl für die Diagnose dieses Codes.
Fahren Sie fort, indem Sie die Spannungs- und Erdungssignale am betreffenden Nockenwellensensor prüfen. Die meisten Fahrzeuge mit OBD-II-Ausstattung verwenden eine Fünf-Volt-Referenz als Basis, prüfen Sie jedoch die Herstellerspezifikationen für Ihr Fahrzeug. Es sollte auch ein Bodensignal vorhanden sein. Eine dritte Schaltung (als Signalschaltung bekannt) liefert ein Signal an das PCM. Es können auch andere Ausgangssignalleitungen vorhanden sein, dies ist jedoch eine grundlegende Übersicht. Überprüfen Sie erneut den Schaltplan (auf All Data DIY zu finden) für Ihr Fahrzeug. Wenn die Referenzspannung und die Erdung innerhalb der Herstellerspezifikationen liegen, fahren Sie mit dem nächsten Schritt fort.
Trennen Sie den elektrischen Stecker vom betreffenden Nockenwellensensor und testen Sie ihn gemäß den Empfehlungen des Herstellers mit dem DVOM. Wenn die Widerstandswerte des Sensors nicht den Angaben des Herstellers entsprechen, ersetzen Sie den Sensor. Wenn alle Widerstandswerte des internen Sensorkreises den Spezifikationen entsprechen, fahren Sie mit dem nächsten Schritt fort.
Schließen Sie den betreffenden Nockenwellensensor wieder an und schließen Sie die positive Prüfleitung des Oszilloskops an die Signalausgangsleitung an. Das Minuskabel an den Erdungskreis des Sensors anschließen. Schalten Sie das Oszilloskop ein und wählen Sie die entsprechende Spannungseinstellung. Beobachten Sie bei laufendem Motor das Wellenformmuster auf dem Oszilloskop. Suchen Sie nach unerwarteten Spitzen oder Störungen im Wellenformmuster. Wenn Sie Spitzen oder Störungen feststellen, wackeln Sie vorsichtig mit dem Kabelbaum und dem Stecker des betreffenden Sensors, um festzustellen, ob das Problem eine lose Verbindung oder ein defekter Sensor ist. Suchen Sie auch nach fehlenden Spannungsblöcken im Wellenformmuster. Wenn es fehlende Blöcke gibt, vermuten Sie ein defektes oder abgenutztes Spurrad oder Zahnrad. Überprüfen Sie auch die Magnetspitze des Nockenwellensensors auf übermäßige Metallrückstände und reinigen Sie sie bei Bedarf. Wenn die Wellenform normal erscheint, fahren Sie mit dem nächsten Schritt fort.
Schließen Sie die Testkabel des Oszilloskops wieder an die gleichen Stromkreise in der Nähe des PCM-Anschlusses an. Beobachten Sie das Wellenformmuster. Wenn es Abweichungen im Wellenformmuster gibt, wie beim Anschließen der Prüfleitungen in der Nähe des Sensors festgestellt wurde, ist ein offener oder kurzgeschlossener Stromkreis zwischen dem Steckverbinder des Nockenwellensensors und dem PCM-Steckverbinder zu vermuten. Trennen Sie die Steckverbinder von allen zugehörigen Controllern und testen Sie die einzelnen Schaltkreise mit dem DVOM. Kurzschluss oder Unterbrechung müssen ersetzt werden. Wenn das Wellenformmuster so aussieht wie beim Anschließen der Messleitungen in der Nähe des Sensors, liegt ein Verdacht auf ein defektes PCM oder einen Programmierfehler vor.
Codes in Bezug auf P0368
Dies ist keine vollständige Liste verwandter Codes.